We Take The Risk Out Of Restoration
Electrostar provides turnkey fire, smoke, and water electronic restoration services to insurance professionals, emergency service providers, facilities managers, business owners, and homeowners.
We are ISO 9001:2015 certified for the evaluation, cleaning, and restoration of electronic equipment impacted by contamination, as well as for training and certifying electronics restoration professionals. Our restoration solutions help companies, organizations, and households solve five of the most common challenges when facing a catastrophe.
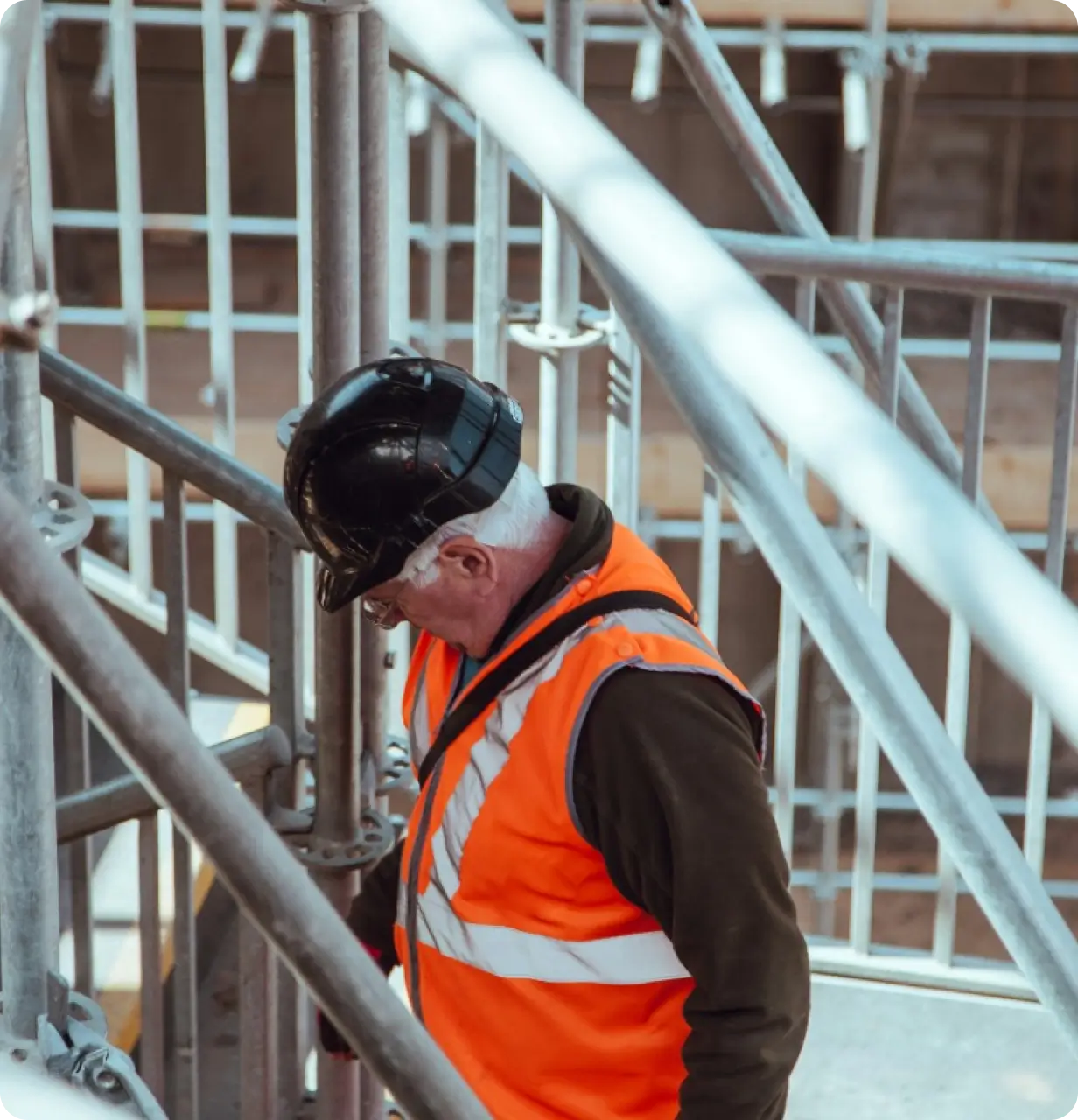
Get back to business seamlessly
Why ELECTROSTAR
Learn how our Certified Technology Restorers™ can get you back in business with a 95%+ recovery rate.
5 Issues Electrostar Restoration Solves
1. Replacement
Obtaining exact replacement equipment can take anywhere from several months to two years, which can significantly impact your ability to meet customer needs and restore operations quickly.
2. Retraining
Extended operational disruptions can lead to the loss of valuable, experienced employees. Introducing new equipment during recovery may require extensive retraining to adapt to new systems, even for seasoned employees.
3. Reprograming
Replacement equipment must be programmed to meet your specific requirements. This procedure goes beyond new computers; it includes manufacturing, telecom, medical equipment, and more, involving loading necessary programs and entering specifications to ensure functionality.
4. Reconfigure
New equipment may have dimensions or configurations different from your current models. Adjustments to your production floor layout, work processes, or infrastructure may be necessary to accommodate these changes.
5. Re-establish
During downtime, customers will seek alternatives for the products or services they need. It's crucial to restart operations as soon as possible to ensure your customers, whether they are diners, patients, or students, can access your offerings without interruption.
5 Issues Electrostar Restoration Solves
1. Replacement
New equipment may have dimensions or configurations different from your current models. Adjustments to your production floor layout, work processes, or infrastructure may be necessary to accommodate these changes.
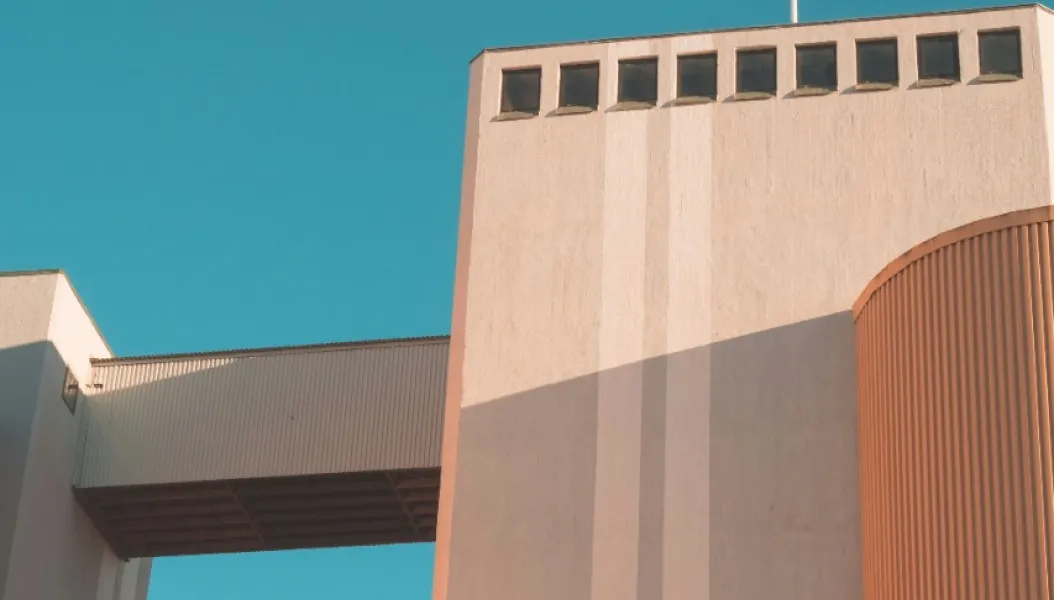
2. Retraining
Extended operational disruptions can lead to the loss of valuable, experienced employees. Introducing new equipment during recovery may require extensive retraining to adapt to new systems, even for seasoned employees.
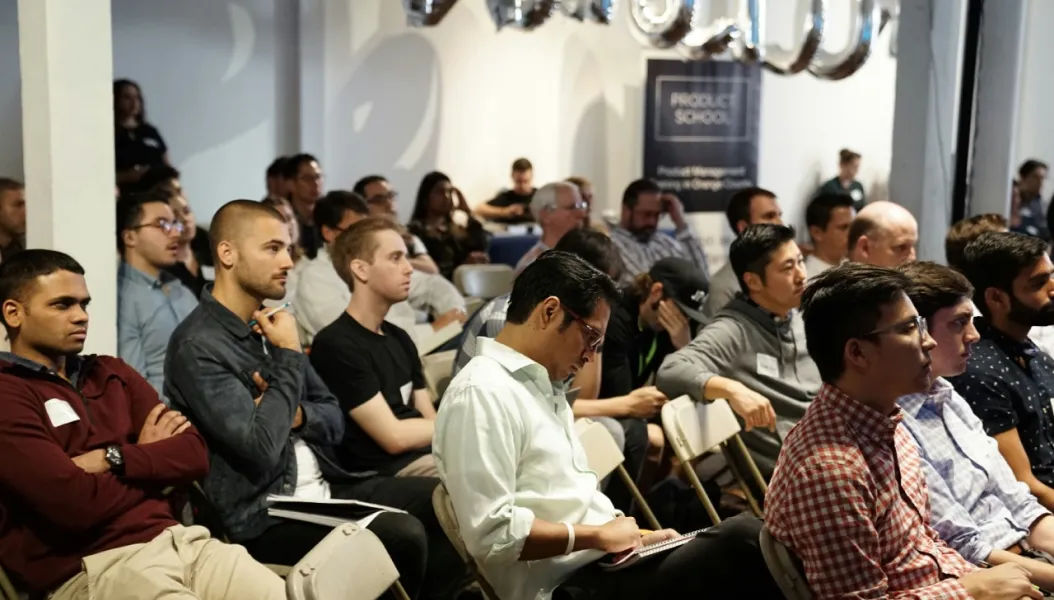
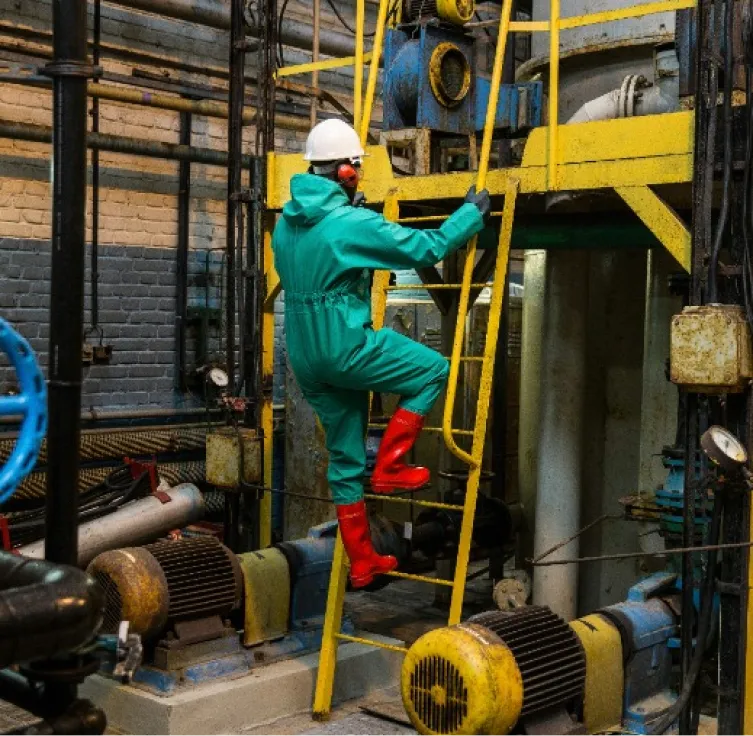
3. Reprogramming
Replacement equipment must be programmed to meet your specific requirements. This procedure goes beyond new computers; it includes manufacturing, telecom, medical equipment, and more, involving loading necessary programs and entering specifications to ensure functionality.
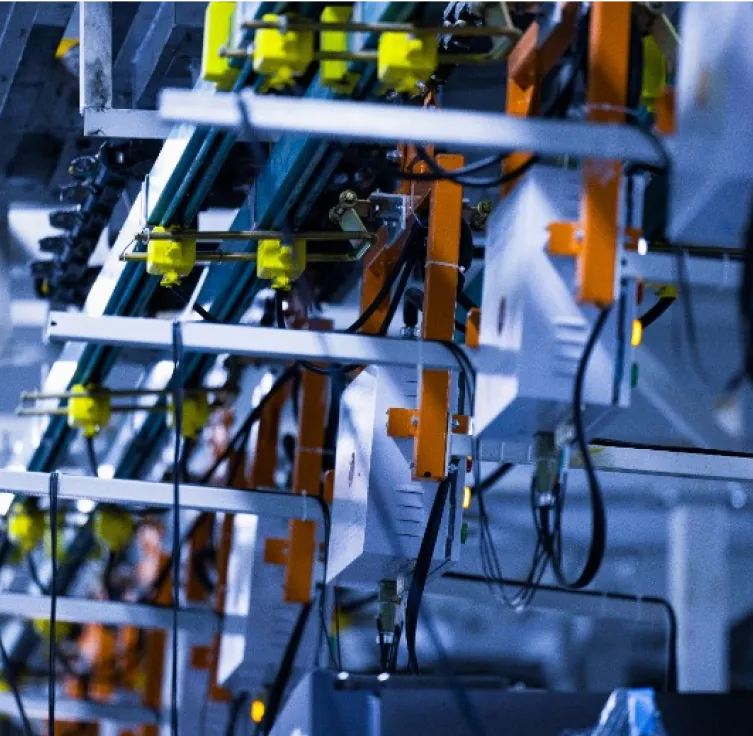
4. Reconfigure
New equipment may have dimensions or configurations different from your current models. Adjustments to your production floor layout, work processes, or infrastructure may be necessary to accommodate these changes.
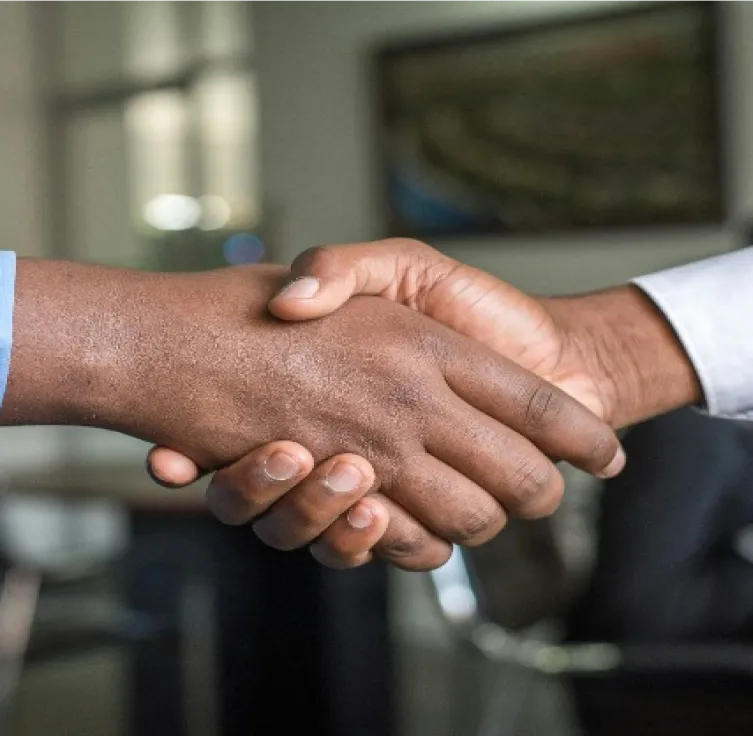
5. Re-establish
During downtime, customers will seek alternatives for the products or services they need. It's crucial to restart operations as soon as possible to ensure your customers, whether they are diners, patients, or students, can access your offerings without interruption.
ELECTROSTAR is committed to restoring your current equipment to better-than-pre-loss condition with a minimum of downtime and interruption.